How 3D Scanning Works
Having remote job site capabilities is no longer “nice to have.” Because of this, 3D scanning has become a staple in the modern construction manager’s toolkit. So how does the technology work and why is it so useful for construction? Here is a brief overview:
How 3D Scanners Capture Site Measurements and Conditions:
3D scanners use laser technology to create exact digital models of a designated area. Using a non-harmful laser, the scanner rotates 360 degrees and connects its beam with the various surfaces and objects in the space.
The scanner uses this information to pinpoint the position of each object and surface relative to the scanner. This data is stored as what is commonly referred to as a “point”. As the scanner picks up millions of these points each minute, it connects them to create a complete digital layout of the room with accuracy down the millimeter, also known as a point cloud.
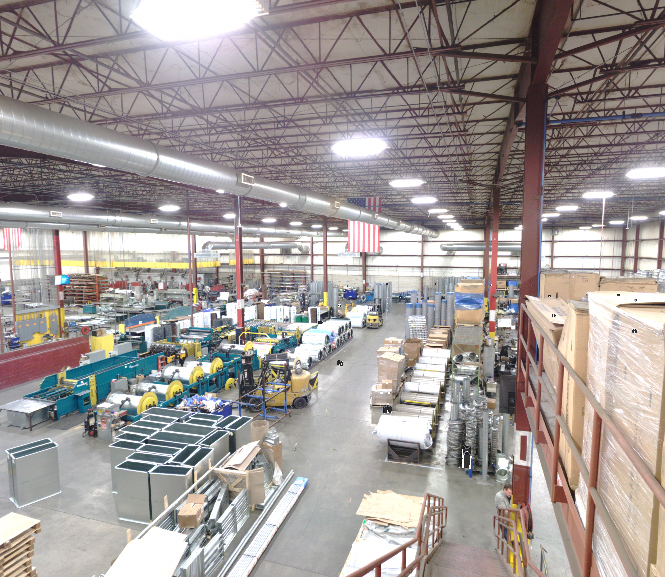
While the scanner is collecting these points, it is also taking high-resolution images of the area. These images are stitched together with the laser’s data to create a real-world view walk-through of the site. This virtual tour is technically precise, populated with the exact measurements taken by the laser, making it easy to assess the smallest details.
3D Scanner Applications In Construction:
Just like other technologies, there are many ways that 3D scanning can be used. Depending on the project’s needs, the tool can drive value in the following ways that span the entire project lifecycle:
As-Built Documentation and Site Verification
Too often as-built documentation is severely out of date or nonexistent. This leads to conflicting project plans and costly delays. With 3D scanning, this no longer needs to be the status quo. After the demolition is complete, general contractors can use a 3D scanner to create new as-built documents and verify the site conditions saving up to 75% on the process.
Scan-to-BIM and Clash Detection
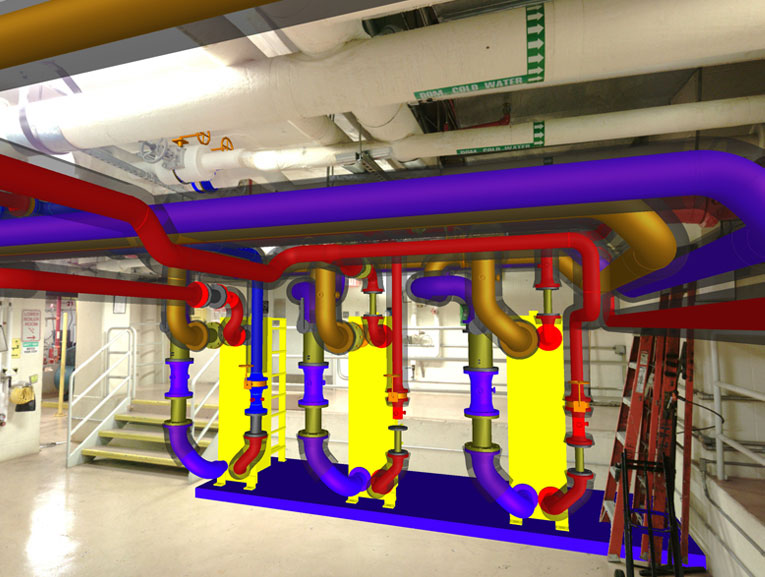
The 3D scan can also be used in unison with Building Information Modeling (BIM) for advanced coordination and clash detection. Using the real-world view walkthrough, drafters can layer in the 3D BIM models to visualize project plans in the space. This makes catching incorrect plans easy. This Scan-to-BIM process empowers trade teams to effectively collaborate and prevent costly disruptions.
Remote Coordination and Measuring
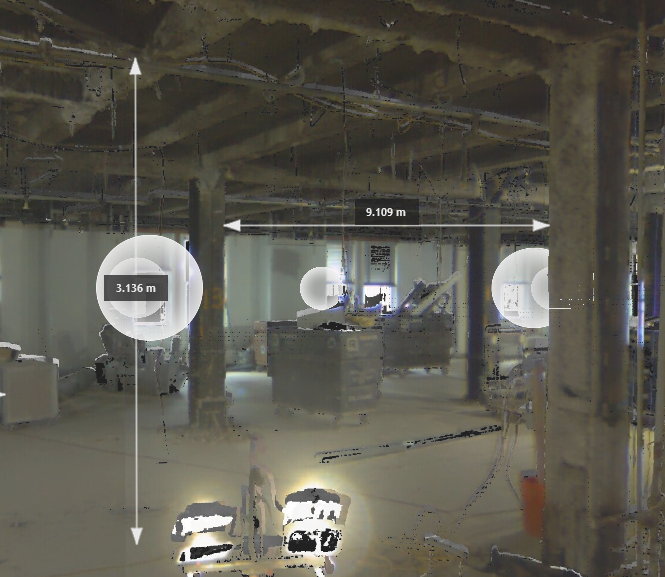
The virtual tour of the project site can also be used to take measurements remotely. Because of the accuracy provided by laser technology, general contractors can have confidence that measurements taken over the internet are correct.
As the COVID-19 pandemic dramatically showed us, having remote work capabilities is extremely valuable to modern day work strategies. With technologies like 3D scanning construction teams do not need to rely as much on their physical location and can shift to a hybrid model of remote and on-site work.
New Construction Project Validation and Progress Work Monitoring
General contractors can also use 3D scanning to prove to clients or regulatory entities that the work done on site matches the approved plans. Because of the remote measurement tool, those viewing the tour can measure and verify that the work matches the plans. 3D scanning makes it easy for management to make ensure that things are coming along smoothly and according to plan.
If you’d like to learn more about 3D laser scanning, reach out to our head of 3D scanning John Brown.