What Are As Built Drawings? Here’s Everything You Need to Know
As built drawings lay the foundation for the final stages of the building life cycle. They clearly depict the finished building structure, accounting for any changes made during construction. This is especially helpful for maintenance and renovation projects, during which operations and maintenance (O&M) staff and construction teams must learn about the existing structure before starting work.
Although as builts are essential, they’re often neglected. Contractors prioritize tasks that directly affect project delivery, saving as builts for later. Despite this, as builts are a vital resource for owners and other stakeholders, helping them understand what was actually built. By elevating the quality of your as built drawings, you have the opportunity to impress clients—improving your company’s reputation and helping you secure more work.
Below, we discuss what as builts are and their importance in construction. We also look at who’s responsible for creating them, and which components should be included. Plus, we’ll give you four tips to improve your as built drawings—helping you streamline your submittal process.
What Are As Built Drawings?
As built drawings, also known as red-line drawings or record drawings, are documents that track changes made to the original building plans as construction progresses. For example, if a contractor installs an additional beam during construction, they must record this change in the as built drawings. This allows owners and other stakeholders to view the final building plans, after all the changes made during construction have taken place.
Why Are As Built Drawings Important?
While not every project will require you to submit as built drawings, it’s still good practice to include them. They are a helpful resource for owners, O&M staff, and future construction teams—providing them with detailed information about the final building plans. This streamlines facility maintenance projects, as Engineered Systems Magazine explains:
“As-built drawings are important for at least two primary purposes. First, they are a record from which future system changes and/or additions can be designed. Second, the as-built drawings can be a valuable tool for the O&M staff. For example, we know that the accurate depiction of shut-off valve locations is considered critical for emergency preparedness.”
In addition to helping with maintenance, as builts also allow architects, engineers, and builders to close out of their projects—leaving behind a legacy of what was built.
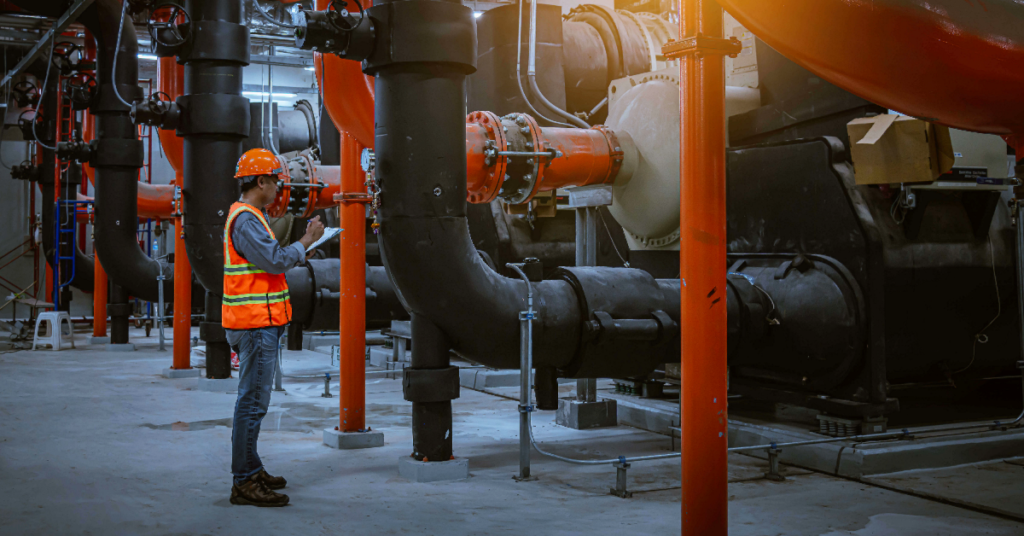
Here are four reasons why as built drawings are important:
- Simplifies renovation projects: By referencing as builts, construction teams can gain a better understanding of existing conditions—allowing them to start work sooner.
- Assists with onboarding: With a complete overview of the final building plans, new teams can access the right information quickly, streamlining the onboarding process.
- Enables land ownership changes: As builts are often required for land ownership changes. They provide new owners with a complete overview of the finished building plans, facilitating the handover process.
- Streamlines facility maintenance: With a complete history of project changes, O&M teams can resolve issues faster, helping owners save money on maintenance costs.
Who Is Responsible for Creating As Built Drawings?
It can be hard to determine who’s responsible for creating as builts. Does the responsibility fall on the architect, who create the original building plans, or on the contractor, who made the changes during construction? According to Cornell University Facilities Services, this depends on whether the original building designs were created in-house or externally, through a contractor:
‘For in-house design jobs … these could be put together by anyone on the design team or the shops,’ whereas for ‘out of house design jobs … the drawings are put together by the contractor, typically with the assistance of sub-contractors for submittal to the architect for inclusion in the record drawings.’
As Built Drawings vs. Record Drawings
As built drawings are often confused with record drawings. While as built drawings are typically created by contractors, record drawings must be prepared by the architect. Record drawings, similar to as built drawings, record changes made during construction. However, these documents must also be reviewed and approved by the architect—making them more reliable than as built drawings.
What Should You Include in Your As Builts?
Need to create as built drawings, but not sure what to include? Here’s a rundown of the most essential components to include in your as builts:
- Material changes: Note any changes made to materials, including their type, size, and location.
- Location changes: Include changes made to the location of doors, windows, plumbing systems, and other major components.
- Obstructions: Note any obstructions encountered, and the solutions used to overcome them.
- Dimension changes: Note any changes made to building dimensions, keeping the scale consistent with what was used in the original drawings.
- Installation changes: Note any changes made during installation to major components like HVAC, electrical, and plumbing.
- Fabrication changes: Record all changes made during fabrication to elements like columns, beams, and staircases.
- Dates: Note the dates when changes were made.
Also, keep in mind that you’re not limited to electronic text documents. Photographs, satellite imagery, and written notes can enhance your as builts, making them easier for others to understand.
4 Tips to Create Quality As Built Drawings
Now that you understand the importance of as builts and what components to include, here are four solid tips to help you improve your as builts.
1. Get an Early Start
As builts are frequently created too late, towards the end of a project. This makes it difficult to create quality as builts, because so many changes have gone undocumented during construction. By getting an early start on your as builts, you can ensure that every change is tracked while construction is taking place. This can help you save significant time and effort—eliminating the need to revisit the site later on to confirm changes.
2. Use 3D Laser Scanning to Speed up the Process
Creating as builts can be overwhelming, especially when you need to account for so many details. This process is made easier with surveying tools like 3D laser scanning, which can be used to capture as built data within minutes. You can use this survey-grade data to streamline your facility updates, expansions, renovation projects, and more.
Don’t want to spend time and money learning how to use a new technology? With our 3D scanning services, we send one of our experts to your project site to capture every inch—helping you save up to 75% on site verification.
Need precise as-built data? Schedule a free consultation with one of our 3D scanning experts here.
3. Be Consistent
As built drawings are frequently inconsistent, making them difficult for others to understand. To make sure your as builts are clear, focus on keeping your notes uniform. For example, keep details like color coding, scaling, and figures the same across all documents. This will ensure your drawings are functional and easily understood—helping owners and O&M teams.
4. Photo-Document Everything
It’s easy to miss critical elements when documenting site conditions. By taking photos of details like walls, floors, and ceilings, you’ll save yourself an unnecessary trip back to the site. It’s also good practice to include elements that are outside of the project site, such as utilities and neighboring buildings, for future reference. By including photos in your as builts, you can make it easier for others to visualize existing structures, which is difficult to achieve using only CAD files. By providing visual data to back up your statements, you can ensure your as builts are readily understood by project stakeholders.
Create Better As Builts Today
Do you need precise as built data for your project? With our 3D scanning services, you can save up to 75% on site verification costs, helping you stay on track and under budget. To learn how our experts can help you quickly capture your existing conditions, request a personalized demo for our 3D scanning services.