Correcting 3 Common Misconceptions of 3D Scanning
Since the pandemic, there have been many discussions about the importance of incorporating 3D scanning into the preconstruction process. The hype surrounding the technology has led to skepticism and a few misconceptions holding back scanning from mainstream adoption. Here is an explanation of the main three:
Myth 1: 3D scanning is too expensive.
Likely this misconception comes from the price tag of commercial 3D scanning technology. High-quality scanners like the ones DJM uses are around $85,000. However, purchasing scanning services is dramatically cheaper like the following New York City example.
In 2018 we were contacted by a general contractor managing a Manhattan skyscraper project. The contractor needed to measure three floors of the skyscraper, a total of 7,500 square feet. He received a quote for the work from one of the skilled trade teams working on the project. The estimate stated that it would cost $2,909 and require two skilled trades workers to work for three eight-hour sessions.
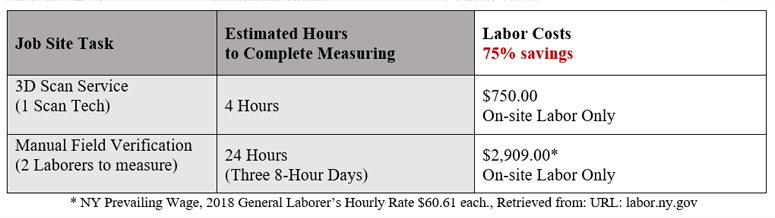
The contractor was anxious to begin the project and did not want to wait three days to get measurements. He asked DJM how long it would take to measure and was surprised that it could be done in four hours and cost a small $750 for the labor. Hiring DJM to scan would save over $2,000 on labor alone.
Labor is not the only benefit. The measurements taken with a scanner are impervious to human error and recorded as a digital map of the area. This prevents miscommunication and inaccurate data that cost the U.S. construction industry more than $31 billion in 2018.
Scanning can help reduce costs in other ways as well. Rework is often referred to as the bane of construction for good reason. The same study cited above found that it can cost up to $177.5 billion in the U.S. annually. Using a scanner to analyze the project site prevents collecting incorrect data that leads to miscommunication and conflict. If you calculate how much rework is eliminated with 3D scanning, the savings far outweigh the service cost.
Myth 2: 3D scanning takes a long time.
Because 3D scans are so data-rich, many believe they take a long time to create. That might have been true a decade ago, but with today’s connectivity, savvy scanning technicians can process scans from the field as they go. This technique allowed DJM to turn around CAD designs for over 33,000 sq. ft. of ductwork in just four days.
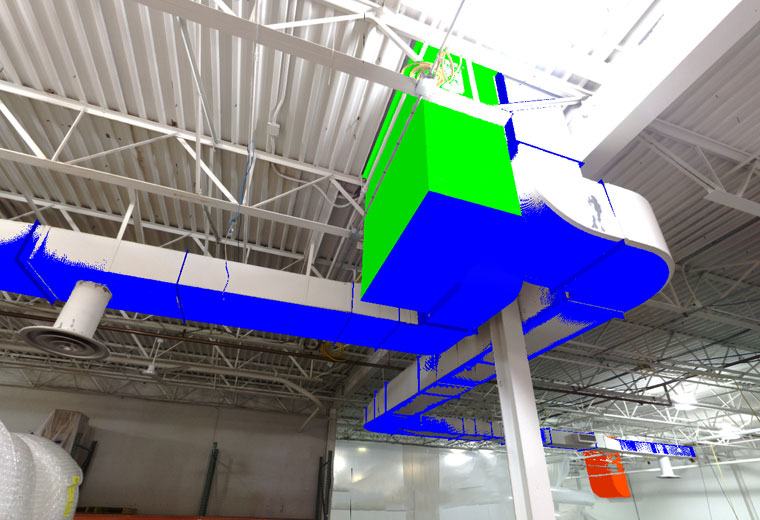
As described in ForConstructionPros, DJM’s head of scanning John Brown would progressively process the scan data as he moved through the facility. Scanning and processing together allowed the draftsmen to begin drafting while the scanning team was still in the field.
In comparison, if the plant had measured the duct manually, the process would have taken three skilled tradesmen and scissor lift around two weeks to measure and document the duct by hand do to its complexity, location, and size. With the scan, the measurements were taken in a day and drawings were completed 3 days later. Contrary to the myth, scanning saves time.
Myth 3: You can only use 3D scanning for measuring.
Scanning is a very diverse technology. It can be applied in a variety of ways across the construction lifecycle and continues to evolve. In both above examples scanning started as a tool for measurement but grew into other areas of the construction process according to the project’s needs. We saw this occur on a large scale with Covid.
The pandemic made it difficult for many contractors to continue operating. The travel restrictions and social distancing mandates added a new layer of coordination and complexity to project sites. Stakeholders looked to 3D scanning for help with remote coordination.
Large-scale construction projects often involve various contractors and subcontractor teams that are based in different locations across the states. Travel restrictions made it difficult for supervisors to fly out to project sites. For one industrial plant, this caused major difficulties when the facility’s main exhaust stack broke.

The supervision team located in Pennsylvania could not fly out to the plant in Georgia. They contacted DJM to scan the facility. “The scan made it feel as though we were standing right in front of the pipe,” – one of the representatives said. Coordinating the plant fixes from within the scan made the process easy. The team could measure, markup, and share viewpoints with the cloud-based file.
As construction shifts towards digital-first experiences, scanning will become a staple in the preconstruction process and likely throughout the project. While it is still bordering on mainstream adoption, it is time to experiment with the technology and grow accustomed to it. As discussed, scanning services are affordable, fast, and useful for construction in many ways.