What Holds the Key to Success for Digital Twins?
The construction industry has been historically slow to adopt emerging technologies. Despite its initial resistance to new technology, there have been recent instances of growth. By 2019, 80% of contractors reported they believed they would incorporate advanced technology by 2022, according to the USG and U.S. Chamber of Commerce Commercial Construction Index. This marks a significant change in the construction industry, as it increasingly relies on new technologies to foster better workplace safety, productivity, and collaboration.
As the construction industry adopts new technologies, it has shifted toward a more collaborative, virtual approach to work. Digital twins are one of the technologies making this shift possible—allowing workers to access information about physical objects through virtual models.
This technology, while it offers many opportunities to improve efficiency and design, relies heavily on the quality of the data it is built from to function efficiently. To implement digital twins successfully, companies must focus on developing a system for collecting accurate data. It is only with precise data that digital twins can operate reliably—otherwise, companies risk creating a digital twin that does not accurately represent the physical structure.
Featured Tool: Free Beginner’s Guide to Laser Scanning [eBook]
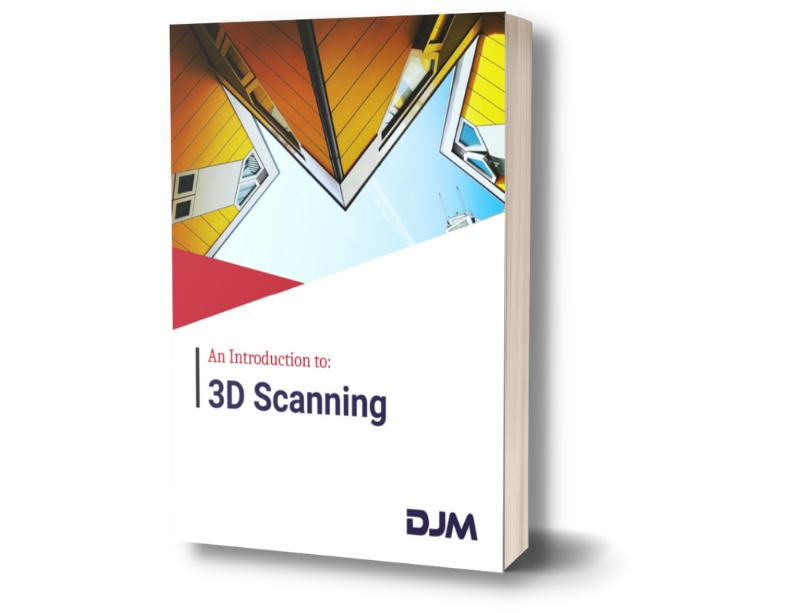
Download the guide to learn more about how laser scanning works, its applications in construction, and how it can help you eliminate RFIs and trade clashes.
Connecting the Physical and Digital Worlds
To create a digital twin, companies take real-world data about an object and recreate the object using a virtual model. Once created, the virtual model can troubleshoot performance issues, run simulations, and identify possible improvements which can be applied to the physical object. Digital twins connect the physical world to the digital one—allowing virtual simulations to predict real-world performance. This capability has revolutionized construction, enabling developers to refine their designs to maximize efficiency.
Developers are catching on to the many benefits offered by digital twins. According to a report published by Gartner, half of large industrial companies will use digital twins by 2021—representing a widespread push in the adoption of this technology.
For companies looking to implement digital twins for the first time, it is difficult to know where to begin. To create a digital twin that makes reliable predictions, companies must first gather accurate measurements of their physical asset. This is an important step in creating a digital twin because it dictates how reliable the digital twin’s predictions will be.
Inaccurate measurements mean that the digital twin will not produce reliable predictions about the physical asset’s performance. This makes it critical for companies to focus on capturing precise data about their physical asset during digital twin creation—otherwise, the digital twin will not fully simulate the physical object.
The Need for Precision in Digital Twin Data
There are three primary stages to the life cycle of a digital twin: development, generation, and operation. The development phase consists of gathering as-built data of the physical asset. This often takes the form of a CAD system or point cloud produced with a laser scanner. The generation stage is when a virtual model of the physical object is created using the data gathered in the first phase. Finally, the digital twin uses real-time data about the physical object to run simulations and predict how it might perform.
The later stages of the digital twin life cycle rely on the accuracy of the data gathered during the development stage. This data contains key information about the as-built environment and is necessary to create a reliable digital twin.
Laser Scanning
To gather accurate data about the as-built environment, many developers turn to laser scanning as a solution. This is because laser scanners can capture field data with a level of accuracy within 1 mm, leaving little room for error. Laser scanners work by gathering digital information about the shape of an object using a non-harmful laser beam. Scans can then be stitched together to create point cloud data, which can be merged into a 3D model in a process known as scan to CAD.

Once the scan data has been collected, the as-built structure can be recreated virtually to form a digital twin. Since as-built measurements give developers the ability to monitor, predict, and diagnose problems with the physical object, data quality is crucial. By using a laser scanner to accurately capture field conditions, developers can ensure that their digital twins are reliable and match as-built conditions exactly.
Although there are other ways to collect field data, most are not optimized for digital twin creation. This is because they are often incapable of capturing all surface points of an object. These alternative forms of measurement are also time consuming, and do not produce the volume of data needed to recreate a physical object virtually. Laser scanning is a more robust form of measurement, capable of fully capturing field conditions and delivering digital twins within minutes.
Creating a Successful Digital Twin Strategy
Companies looking to remain competitive are increasingly turning to digital twins to optimize design and drive better performance. To create a reliable digital twin, however, accurate-as built data is critical. By using laser scanning to capture as-built conditions, companies can ensure that their digital twins are reliable and can predict real-world performance.
Successfully implementing a digital twin requires precise as-built measurements. With our laser scanning capabilities, we can ensure that your measurements are exact—helping you create a reliable digital twin. Contact us today to discuss your needs for digital twin creation, and how 3D scanning can expedite that process. We look forward to hearing from you!
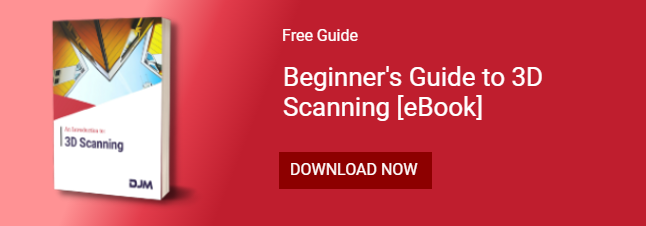