4 Major Benefits of Using Point Clouds in Construction
Point clouds provide valuable data for professionals in the construction industry. The flexibility and precision of point cloud data make it ideal for many construction projects, including digital twin creation and site monitoring. But what is point cloud data, and what are the benefits of using it? In this post, we will first define point clouds—explaining what they are and how they can be captured. We will also describe four ways point clouds are being used across the construction life cycle to increase productivity, improve coordination, and reduce costs.
What Is a Point Cloud?
A point cloud is a set of data points used to represent a physical object or space. Point clouds are made up of millions of individual measurements, each containing an x, y, and z coordinate. Once a point cloud is created, it can be converted into a mesh or 3D model for further use. 3D Models generated from point clouds are precise—making point clouds a reliable way to capture as-built conditions.
How Are Point Clouds Created?
There are two primary methods of capturing point clouds: through laser scanning or photogrammetry.
Laser scanning is the most comprehensive way to create a point cloud. Laser scanners work by using a laser beam to capture digital information about an object. This is achieved by rotating the scanner 360 degrees and connecting the beam with surfaces in the area being scanned. The scanner then uses this information to capture the exact location of objects relative to its position.
Laser scanners provide the speed and level of accuracy needed for most building documentation projects. They allow contractors to easily access scan data, which can be updated as the project progresses. This makes laser scanning ideal for site monitoring, especially when there is a limited window in which site capture can take place, which is often the case in active sites like factories.
→Download Now: Beginner’s Guide to 3D Scanning [eBook]
Photogrammetry is different from laser scanning in that it’s a technique, as opposed to a tool. This technique uses a compilation of photographs to generate measurements. To create a point cloud using photogrammetry, you would first take photos of an object at different locations, and then triangulate points on the object and plot them in 3D space. Although photogrammetry is preferred in certain cases, such as when using a drone, laser scanning remains the most accurate way to capture site conditions.
What Are Four Major Benefits of Using Point Clouds?
Point clouds have a range of applications in construction due to their high accuracy levels. Because point cloud data is so valuable, construction professionals have begun integrating it into their projects to improve efficiency and reduce costs.
Here’s a look into how point clouds are being used across the industry:
1. Building Information Modeling (BIM)
One of the primary ways point cloud data is used is when generating Building Information Models (BIM). BIM is a process for creating and managing all the information about a project, leading to the creation of a Building Information Model. BIM provides stakeholders with a way to collaborate across the project’s life cycle, from planning and design to construction and operations.
Laser scanners are used to create BIM models in a process known as scan-to-BIM. In this process, technicians use laser scanning to capture a high-density point cloud of the built asset. Next, the point cloud data is imported into modeling software such as AutoCAD or Navisworks. Here, the data serves as a dimensioned template of the site from which a 3D model can be constructed. Point clouds are used for BIM because they accurately capture as-built conditions—producing exact measurements down to the millimeter. This ensures the BIM model fully reflects as-built conditions, reducing potential rework due to inaccurate plans.
Point cloud data can be used to create new building information models or update existing models with new data. Using your building information model as a reference, you can compare the as-built conditions of the building against the as-designed plans, identifying trade clashes and other errors.
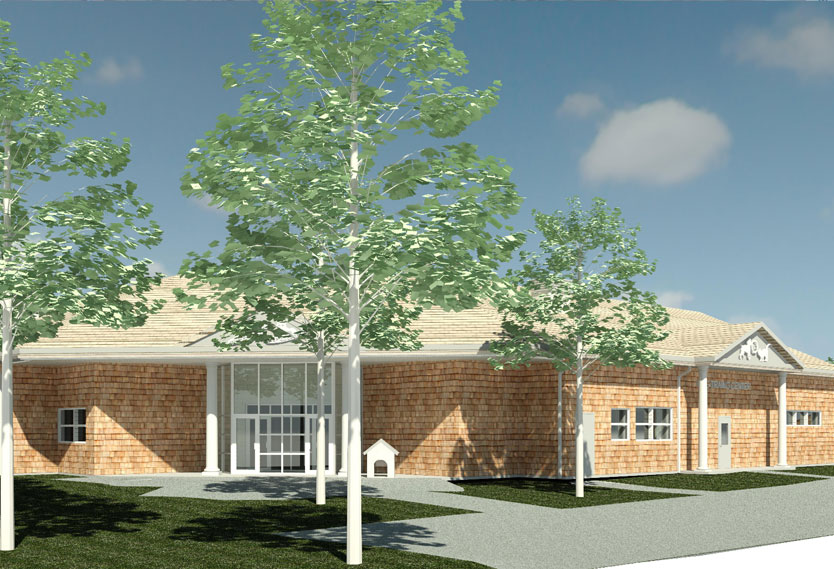
2. Digital Twin Creation
Point clouds are also used to create digital twins. Digital twins are virtual representations of physical objects or systems. The key difference between BIM and digital twins is how the technologies are used. Digital twins, unlike BIM, are used for facility maintenance and operations. They incorporate live data with the use of internet of things (IoT) sensors to monitor real-world performance of the asset. This means they can be used to review information about the asset, in addition to monitoring, analytics, and simulation.
Creating digital twins often requires assistance from a skilled technician. To generate a digital twin, the physical asset must first be captured, typically with a laser scanner. Finally, the asset is digitized, and a digital twin developed that meets your specifications.
3. Site Monitoring
Point clouds can also be used for site monitoring—providing a quick, comprehensive overview of construction progress. If you generate point clouds at regular intervals during construction, you can track what work is completed, when it is completed, and where. This is valuable insight for stakeholders, allowing them to closely track building progress.
4. Floor Planning
Another common use for point clouds is creating floor plans. Once a point cloud of an asset is created, drafters can trace the floor plan using CAD or floor-planning software. This method of generating floor plans is more efficient than traditional methods, like total stations or laser distos.
Learn More About Point Clouds
Construction professionals are using point clouds to improve their workflows—shortening turnaround times and reducing costs. Whether you need to capture as-built conditions or monitor construction progress, point clouds give you the accurate measurements you need to stay on schedule. To learn how to integrate point clouds into your next project, download our free guide to 3D scanning.
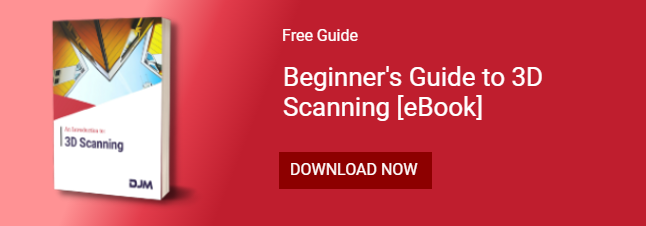