Full-Service CAD with DJM
A Summary of Our Discussion on Brewing with BIM
Are point clouds garbage data? Should scanning be in-house or contracted out? What will consumer ConTech do to the industry? These are the questions that DJM’s Tim Libman and John Brown pondered with David Campbell and Joseph Whitney of Brewing with BIM. After over an hour of discussion and some spiced rum, here is what we learned:
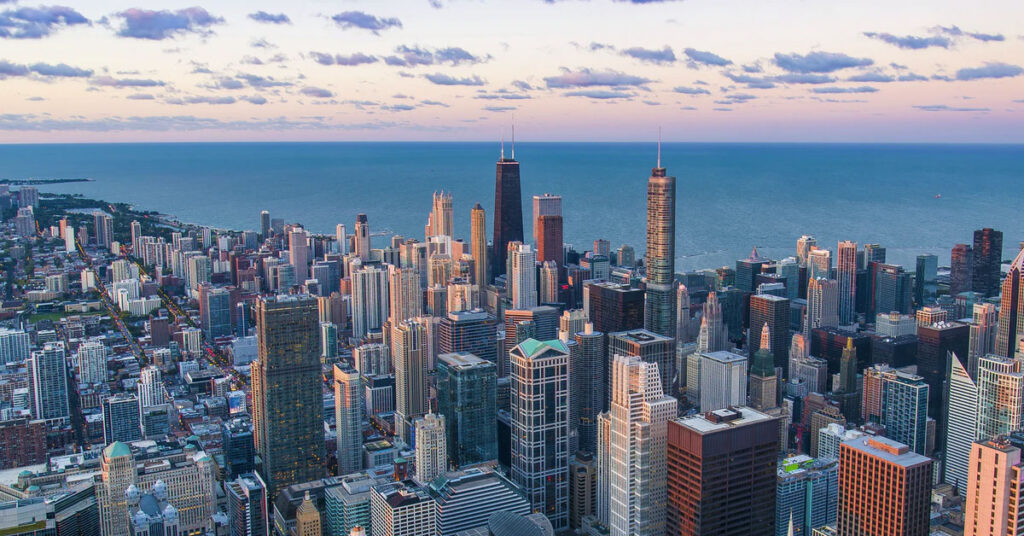
Scan to BIM is Growing Strong in Coastal Metropolitan Hot Spots
After discussing a few personal experiences with clients, the round table realized that scanning seems to have taken off in metropolitan hot spots along both coasts. John related how his reach initially started in New York, Philadelphia, Baltimore, and Washington D.C. and then spread out to cities in the North and South. Dave and Joey related that they see a similar pattern of adoption in metropolitan areas on the Pacific Northwest that is slowly growing to the center of the country.
Each agreed that this made sense as the value of scanning was early realized on large scale builds but has taken longer to actualize in suburban and smaller-scale projects. An Indiana native, Dave shared that he believes this has caused scanning to take longer to adopt in rural areas. “You’re not scanning the cornfields?” teased John.
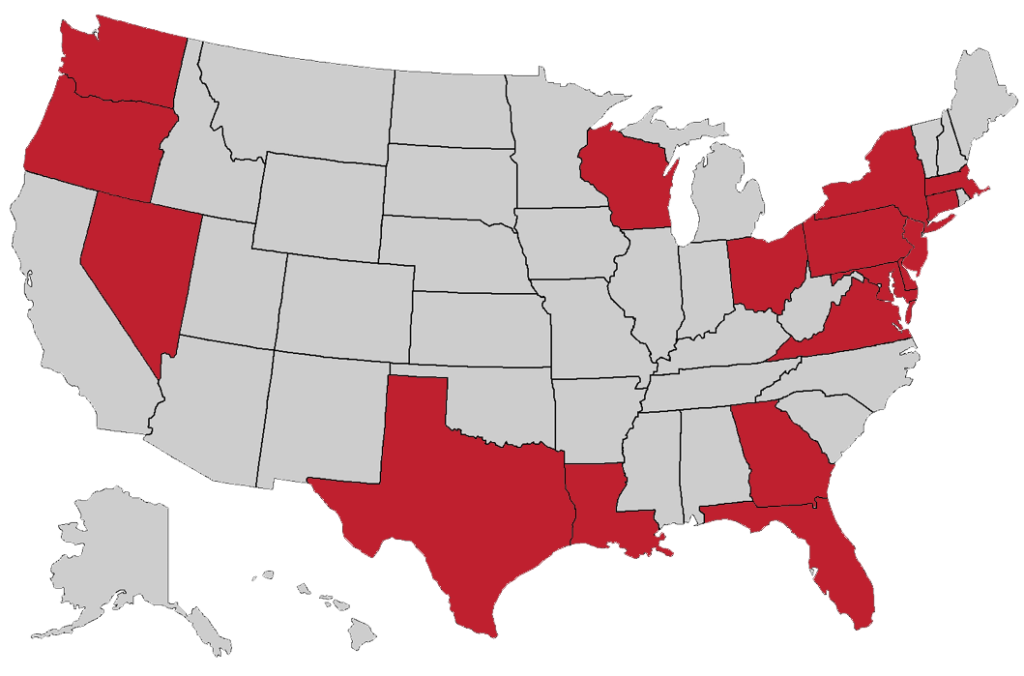
COVID Has Accelerated the Adoption of 3D Scanning
Jokes aside, 3D scanning has taken off in the past year, and the COVID crisis has accelerated its adoption in unexpected areas. Now that remote coordination is no longer a nice to have, stakeholders throughout the construction process have realized the technology’s value. “You’re able to go to a job site without having to go to a job site,” summarized John. Each agreed that the COVID crisis opened eyes to the benefits from the client’s side of things.
It goes hand in hand with the virtual way people are doing business
– Tim Libman, Project Manager DJM
Past the COVID crisis, Tim pointed out that scanning has value. “It goes hand in hand with the virtual way people are doing business,” he added. Instead of hopping on a plane and traveling to a site, project stakeholders can receive a link to the site. Having the ability to collaborate online will only increase in value as working from home continues to grow, and teams keep spreading out across the country.
To further express this point, Tim shared a recent project which included team members from Chicago, PA, and Georgia. By showing scans of the project site and BIM models of proposed changes, the team coordinated and made decisions from the comfort of their homes. Tim, John, Dave, and Joey all agreed that this level of visualization causes the project to move faster than originally possible, even amidst COVID. “They are asking questions in the design phase that they normally wouldn’t have until the install,” Tim further explained.
Unless Companies have a Dedicated Scanning Team, it Makes Sense to Contract Out
As scanning grows in popularity, the question arose, should companies invest in scanning equipment? Dave, Joey, Tim, and John all shared the opinion that although the cost of scanning equipment and software has come down, it still makes sense to contract the service out.
John went on to share his opinion that having trained staff is more important than having the technology accessible. “Who is doing the scanning?” asked John. “It’s not brain surgery,” joked John, “but do they know what to look for?” John mentioned concerns that companies focus too much on the equipment and fall short of training their team on the construction process. “Are they comfortable navigating the site? Are there certain points in the building they need to capture? Is there existing ductwork?” Understanding what is needed and how it will translate to the next stage of the project is equally critical.
Dave echoed John’s sentiments with an experience he had recently. “I’m working with a scan right now where someone just moved the scanner around which is alright, but at the same time they didn’t have enough overlap in portions of the building.” After messing around with the scan for hours, Dave realized that it was unusable for his purpose. “I’ve spent like 2 hours trying to put this scan together, but I can’t, I need them to go out and redo this.”
Know What is Needed Before the Scan
There are a lot of nuances to scanning technology, so it makes sense that technicians unfamiliar with the equipment would set things up incorrectly. These nuances make it necessary to figure out the purpose of the scan before performing it. By discovering its purpose first, the technicians set up the scanner to capture the right things.
I’ve actually said to people I don’t think scanning is a fit for what you need here.
– John Brown, Head of Scanning DJM
David and Joey mentioned that they experience people who receive a scan and question the quality of the data, but the real issue is that they did not understand what they needed. They inevitably receive the wrong service. John chimed in, “I’ve actually said to people I don’t think scanning is a fit for what you need here.” He reiterated that scanning is used for verification, modeling the structure, and even to make sure floor to slab heights are correct. But at the end of the day, John said it’s a matter of “what they need and why.”
To get the full experience, grab your favorite brew and listen to the full podcast here.