3D Printing and Construction: How Additive Manufacturing Could Change the Industry
3D printing and the implications of the technology have been a hot topic in construction for several years now. Certain projects like Apis Cor’s 3D printed house that was completed in 24 hours and MX3D’s metal smart bridge have drawn a lot of media attention. But does the technology live up to the hype? While we are still far away from widespread adoption, here are three ways the technology could fundamentally change the construction industry.
1. Increased productivity with 3D printing:
Construction projects are complex and require a lot of coordination and time to complete. A survey from Home Advisor found that on average custom home projects take four months or more to finish. For more complex projects, these timelines can extend to over a full year (depending on if there are any hiccups). Data from McKinsey shows that 98% of mega construction jobs can expect to run over estimated deadlines by 30%. These statistics and more bring to light an obvious opportunity for improved productivity across the project lifecycle. While it is not an end all be all, technologists are hopeful that 3D printing will improve project workflows and help to fix this problem. Currently, costs associated with the technology will likely prevent large scale adoption of 3D printing for another decade or so.
2. Reduced Project Hiccups:
When looking at the history of construction, Building Information Modeling (BIM) and 3D modeling have been some of the most revolutionary technologies. Before BIM, construction teams were limited to troubleshooting and coordinating project plans in 2D. This limited collaboration across teams caused frequent errors and hiccups to occur on the job site, often incurring unforeseen additional expenses. Now with the use of BIM models, teams examine plans and catch trade clashes ahead of time, significantly reducing the number of errors. Many believe that large scale 3D printing could take construction BIM a step further, enabling entire projects to be printed from the 3D model. Certain high profile projects, like Icon’s community in Mexico printed entirely by their Vulcan II, have given life to that dream.
3. Sustainability:
Because 3D printing has the potential to improve the way construction materials are used, the technology would also likely reduce the waste of any project utilizing it. Data reported by the EPA estimates that somewhere between 230 to 530 million tons of construction waste is produced by the US annually. Finding more sustainable construction practices is a big concern for stakeholders. In theory, 3D printers using perfectly dimensioned BIM models could print structures with the exact amount of materials needed, dramatically cutting back on the amount of materials sent to landfills. As stated in a study featured on Science Direct, BIM modeled and 3D printed houses are the “sustainable houses of the future.”
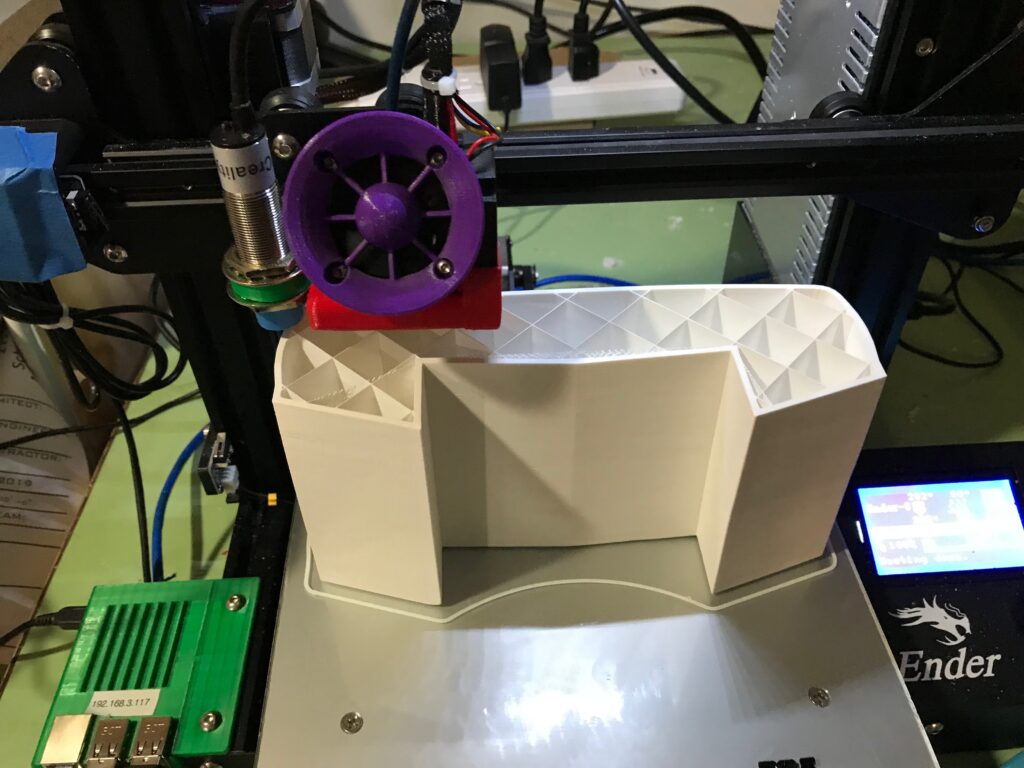
3D printing still has a ways to go:
While the technology holds a lot of promise, the high cost associated with 3D printing robotics has kept it from being put into practice on a larger scale. Additionally, if construction printing is to take off, there is a big need for robotics professionals. Like the skilled trades gap, there is a severe lack of qualified 3D professionals in the industry. We are still a long way off from large scale adoption, but the opportunity is there. Construction is ready for some 3D printing disruption.