Smarter Not Harder: 3 Tips for Reducing the Cost of Rework During Renovation Projects
Over the past two decades, technological advancements have made a positive financial impact on the construction industry. Digitization and cloud connectivity have optimized outdated processes and brought much-needed improvement to project workflows. While significant strides have been made, rework still ads up to as much as 4.2 billion in the US alone. Consider these three tips to reduce the cost of rework for your organization.
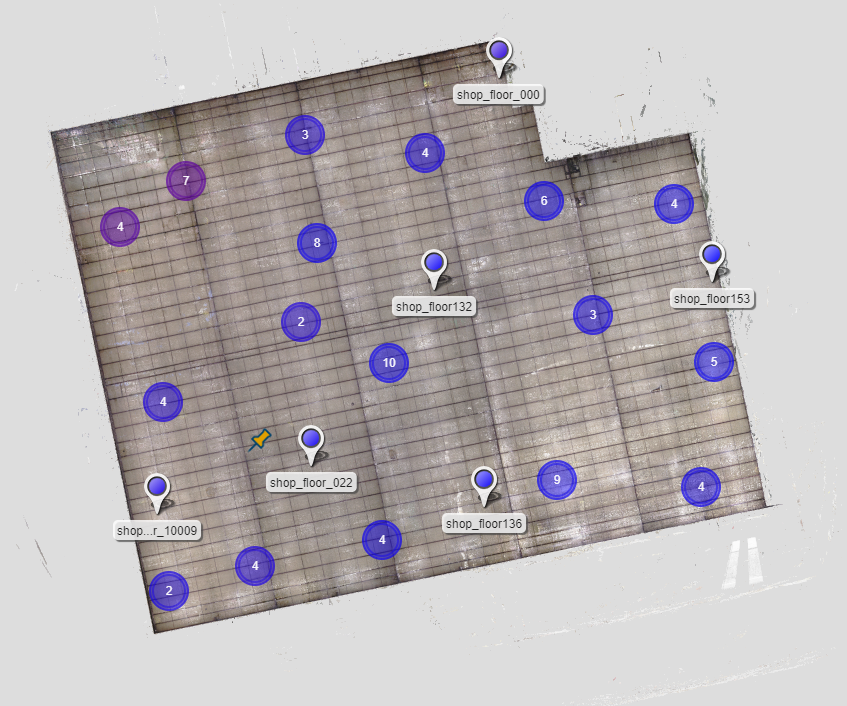
1. Create Up-To-Date As-Built Documentation
Before starting the project, stakeholders need to understand exactly what they are getting into. Without up-to-date site conditions and measurements, design mistakes and work order changes are inevitable. To prevent these and make sure the project timeline stays on track, an accurate as-built model should be created.
Having an updated as-built ensures that project specialties base their plans on the actual measurements and structural layout. It also informs stakeholders if the site has had any structural changes made. Having this documentation also ensures that any manufactured components fit correctly the first time they are installed. This prevents wasted man-hours and materials.
Capturing as-built documentation is no longer a time-consuming task. Today with a 3D scanner, project leads can digitize project sites and create updated blueprints that are accurate within a fraction of an inch. This 3D real-world documentation can be shared through the cloud to measure and view the site from anywhere.
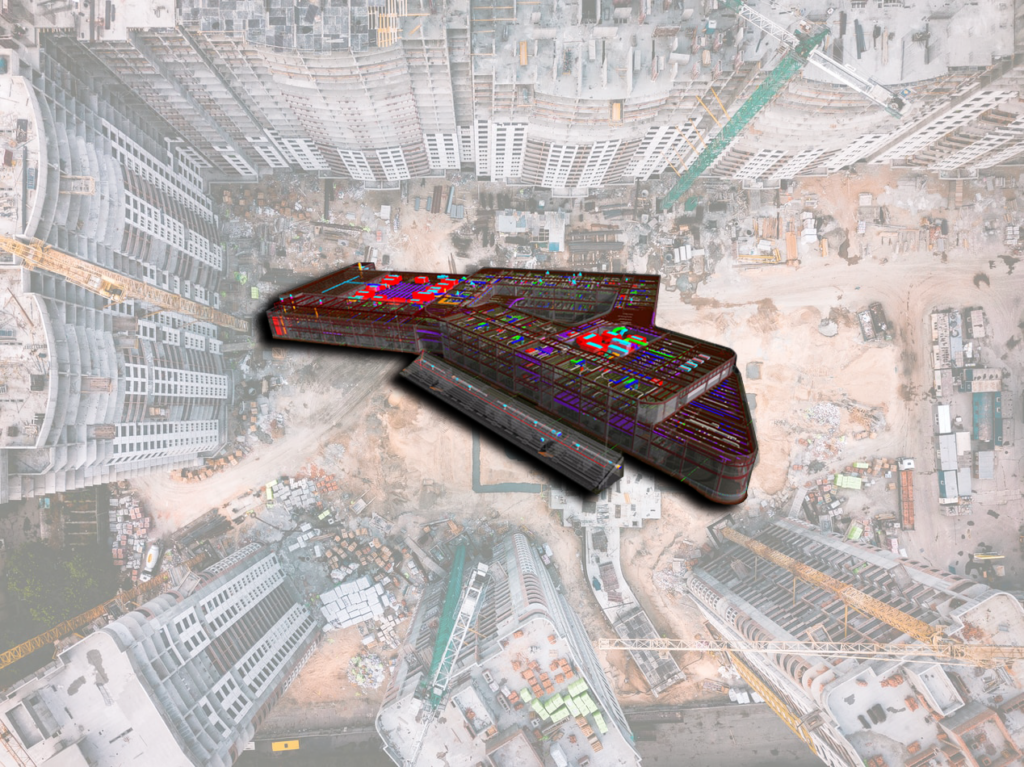
2. Create a Central Model of the Construction Project
Construction projects are complex and require many different trades to work together to bring the job to completion. Typically each trade involved will create plans independently of each other. Because each team is unaware of the other’s ideas, drawings will often clash and unsurprisingly lead to job site conflicts. Small mistakes that could have been avoided add up to thousands in unnecessary costs, additional man-hours, and change orders. While it is understandable that some details will fall through the cracks, obvious trade conflicts should be addressed before construction begins. This is why Building Information Modeling (BIM) is a worthwhile investment.
By using a BIM model, any point of friction between the plans is identified and remedied before the build begins. All stakeholders involved in the project collaborate over a central model and can easily discuss implementing changes to prevent hiccups. A recent survey from Procore shows that this extra step saves construction companies 25% in labor costs. A survey highlighted on Plangrid’s productivity blog shows that BIM can reduce rework by 46%. BIM may appear to be an additional line item but more than pays for itself in time and rework cost savings.
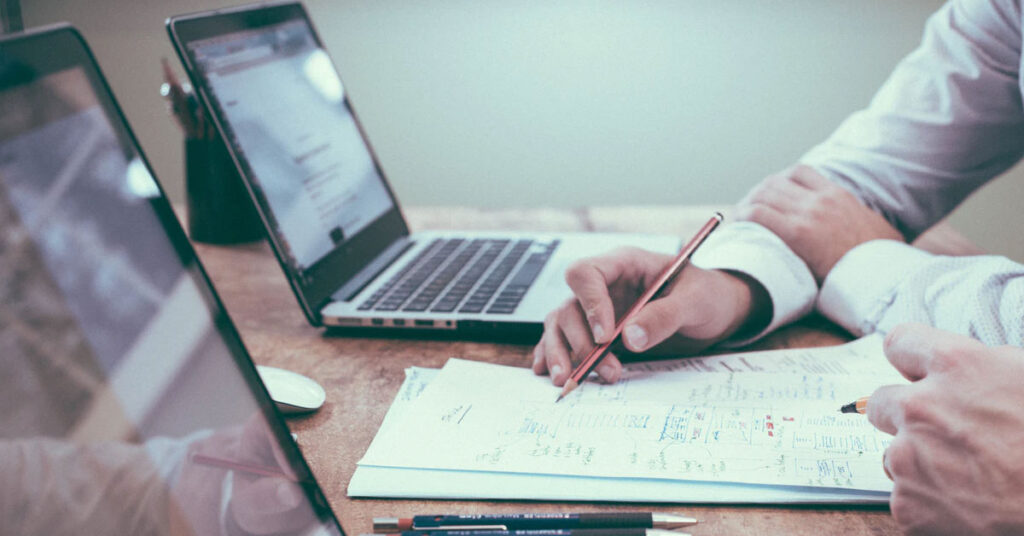
3. Hire Coordination Specialists
While starting the project off with an updated as-built and central project model cuts back on the number of possible hiccups, there is still a lot of coordination that needs to happen between teams to make sure things run smoothly. Along with making sure that the approved plans are followed, any minor changes that are made to the build need to be approved and communicated across trades. This level of management requires an entirely different set of skills and is why hiring an outside coordination firm is a good idea.
Project coordination specialists have an in-depth knowledge of each trade, but can also speak to the overall scope of work, timeline, budget, and potential regulatory issues. They excel at inter-team communication and will work behind the scenes to make sure trades are collaborating and working efficiently. Miscommunication or lack thereof causes on average 52% of rework. Having an outside coordination team to corral and communicate throughout the project gives stakeholders a central point person and pays off in the long run.
Disconnected construction workflows are becoming unacceptable. While once considered a necessary evil, teams that have adopted new technologies and provided a better overall experience are proving that working smarter not harder has financial benefits. Companies that want to compete in this new era of construction will need to follow suit.