How 3D Laser Scanning Supercharges Troubleshooting
How 3D laser scanning empowers quick fixes
This article was originally published by John Brown on LinkedIn Pulse.

With DJM’s 3D Laser Scanning services, a rural manufacturing facility was able to design fixes to their main exhaust stack without disrupting operations. The break, caused by a misalignment of duct, was located between the pipe’s base and connection point to the main duct line. Fixing the issue would require a crane and temporary facility shutdowns.
Because fixing the stack would cause so much disruption, the facility’s management team wanted to make sure the repair plans were correct. Unfortunately, the team located almost a thousand miles away, could not travel to examine the damage. The stress of COVID-related travel restrictions made it near impossible to coordinate the trip. Instead, they reached out to our scanning team for assistance.
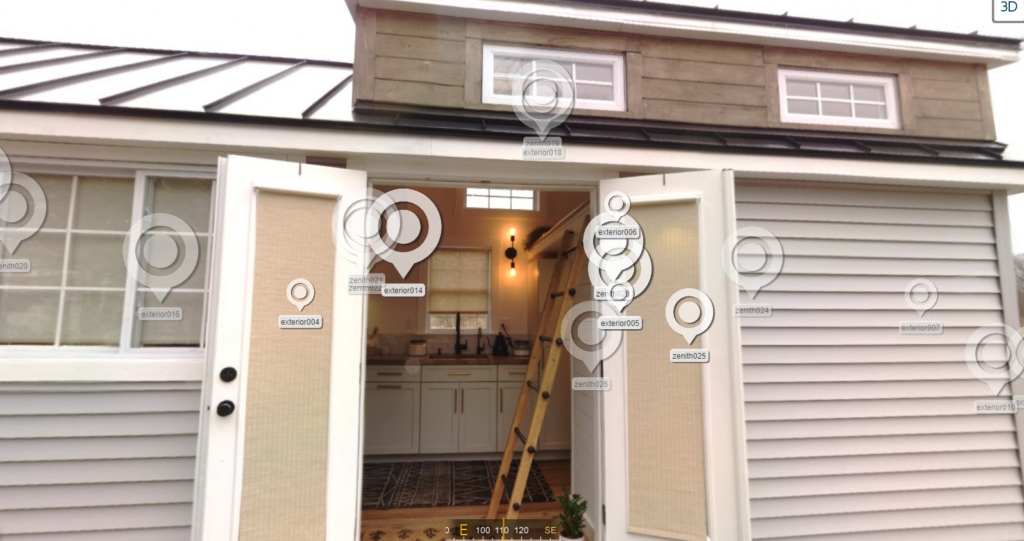
The power of digital twins
The management team wanted a digital twin of the break to coordinate the repairs from the convenience of their office. The scanner captured the exact dimensions and details of the break and surrounding area with advanced laser technology and a high-resolution camera. The data was converted into a photorealistic tour for taking additional measurements as needed. One of their representatives even said, “The scan made it feel as though we were standing right in front of the pipe.”
Now that the team had a virtual replica, it was time to start designing repairs. Both the base and connection point of the pipe required extensive changes. Using the scan, DJM’s BIM draftsmen designed new equipment to fix the issue. When complete, the DJM team then layered in the 3D designs into the virtual tour to confirm that the equipment would work well with the rest of the structure.
The ROI of 3D Laser Scanning
While laser scanning has gained popularity in the past few years, it is still relatively new. Like other emergent technologies, there is skepticism as to its effectiveness and ROI. In this scenario, the manufacturing facility team reported five main benefits. Here they are:
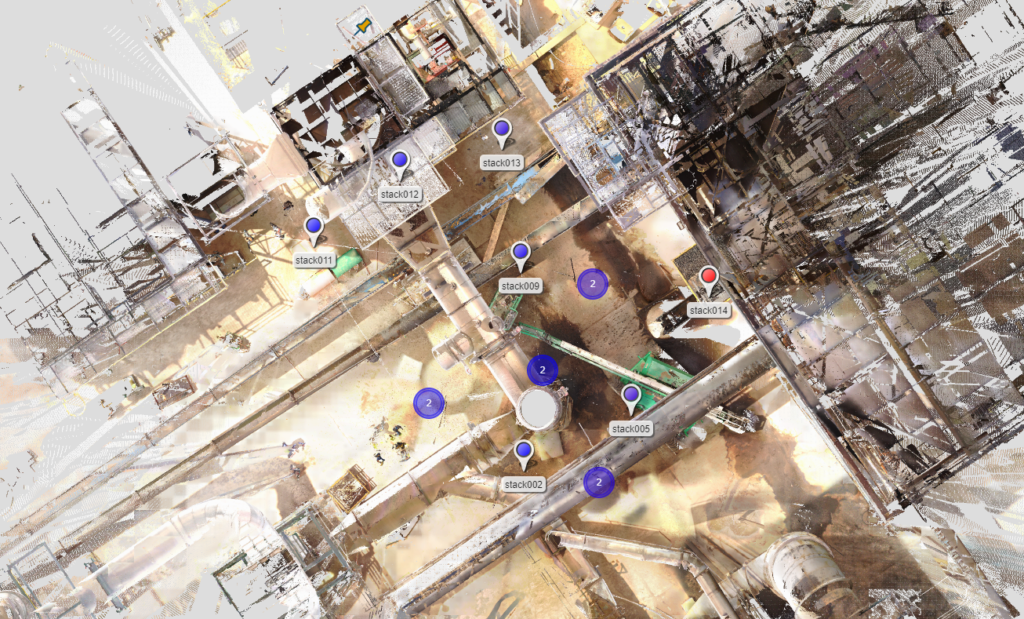
1: Remote Coordination
Many would plan on visiting a site in person to measure and coordinate plans. The COVID crisis called this practice into question and forced industry stakeholders to consider whether in-person operations were the most efficient. It has been since realized that some of the industry’s standard business practices were outdated and needed adjustments to fit today’s level of connectivity and remote capabilities. With the 3D scanning and BIM technology available today, traveling for coordination and management can be a rare occurrence.
Using these technologies saves travel and labor costs, but more importantly, it assists in advanced coordination throughout the entire construction process. For teams separated by distance or working on a project far away, the ability to visit the construction site whenever needed provides value again and again. Having a 3D real world view of the site ads a whole new layer of clarity to coordinating trades.
2: Reduced Rework
Rework is the time and money drain that is the bane of every construction project. In a survey sited by Autodesk, 70% of rework is the result of bad design. While scanning cannot prevent all design errors, it can make sure that the measurements and blueprints that the plans are based off are accurate and up to date.
Often this is half (if not more) of the battle. Incorrect measurements and outdated as-built documentation are frequent causes of faulty designs. These designs have a cascading negative effect on the project lifecycle and can end up breaking the financial health of the project with work order changes and RFIs. Using 3D scanning at the very beginning of the construction process to capture an exact digital replica of the site can prevent a lot of these issues.
3: Less Wasted Workhours
With rework removed, skilled trades can focus on the jobs that matter. A survey from PlanGrid and FMI Corp found that inaccurate information amounts to an estimated $177 billion in additional work hours annually for U.S. construction. Construction workers spend this time fixing mistakes and managing conflicts caused by inaccurate data. Capture the correct information with a scanner prevents much of this wasted time.
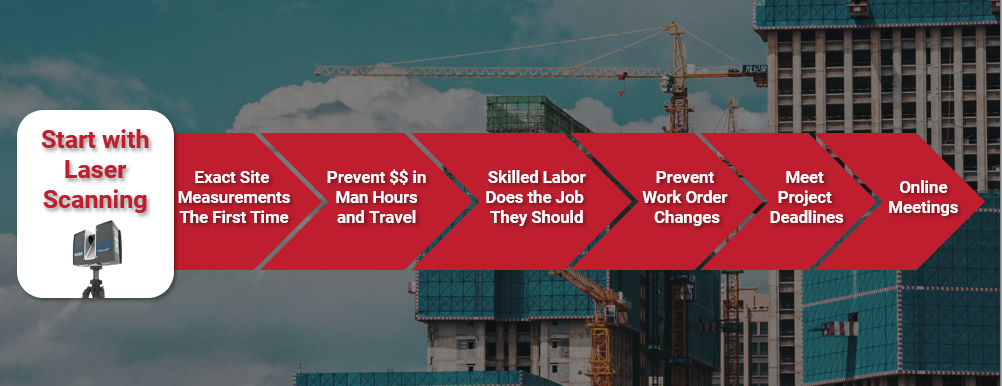
4: Sticking to the Estimated Timeline with 3D Laser Scanning
The benefits of reduced rework and wasted trade hours also have a positive effect on the overall timeline of the construction process. In construction, the phrase “time is money” is more apt than in other industries. Sticking to the deadlines put forth in estimates is critical to making a profit. By eliminating unnecessary rework and ensuring that skilled trades have the freedom to focus on the correct tasks, the lifecycle carries on as planned, and the bottom line suffers fewer unforeseen costs.
All these benefits add up to optimized operations. The forced digital transformation caused by the coronavirus pandemic was unpleasant and even painful for some. Amidst the chaos, remote work, and other glaring opportunities, were noticed. Since the coronavirus pandemic outbreak, industries across the board have had to rethink fundamental strategies. As stakeholders continue to adapt to the new normal and emergent technologies change the industry, construction will show the resiliency and adaptability it has come to be known for.