The ROI of 3D Scanning: Is it Worth it?
Originally published by John Brown on LinkedIn Pulse
I have recently had a lot of questions regarding the ROI of 3D scanning technology. People want to know if the services is really worth it and if the benefits outweigh the initial cost. Much like any other technology, there is a lot of hype surrounding it, so I understand the skepticism. Scanning however, is much more than just a trend, and does benefit the entire construction lifecycle in these five ways:
1: Site Measurements with 3D scanning
Measuring the construction site, while considered one of the most menial tasks of the project lifecycle, is one of the most critical. Measurements are the foundation that all other project components are built upon. Measuring by hand is tedious and depending on the site could require 2 tradesmen multiple days to complete. Not only is this inefficient, but mistakes are common and even likely. Verifying the site manually could lead to remeasuring and often rework.
This is where 3D scanning delivers a lot of its value. With 3D scanning, there is no remeasuring or rework necessary. The laser and smart technology powering the scanner makes sure things are exact the first time and even makes it possible to go back virtual and take additional measurements if you need by creating a digital model of the space.
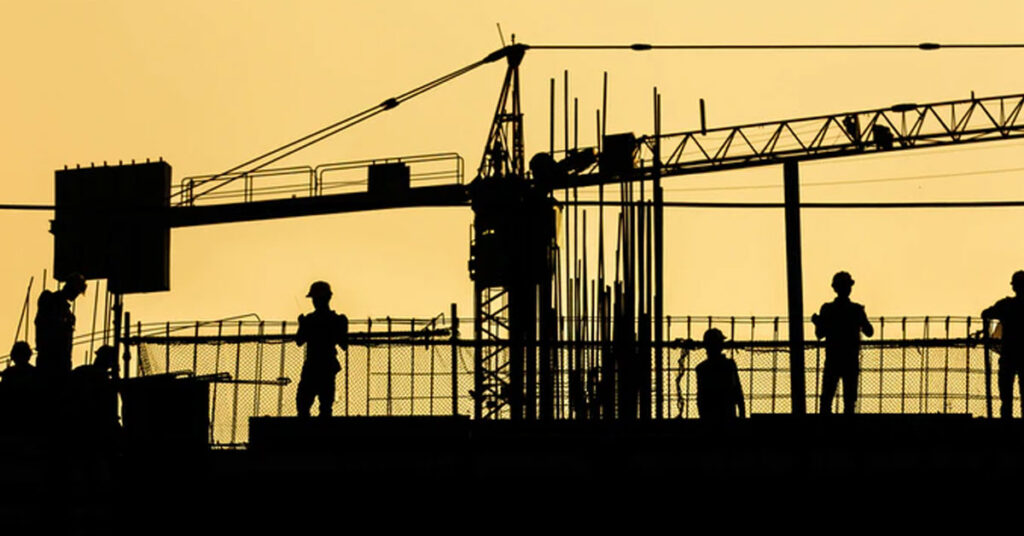
2: Man-hours
While the industry has gotten much more efficient, construction workers’ time is still wasted due to inaccuracies. A survey from PlanGrid and FMI Corp estimated that inaccurate information amounts to $177 billion in additional man-hours annually for U.S. construction. These man-hours are spent fixing mistakes, looking for missing project data, and managing conflicts caused by inaccurate data. While it cannot prevent all this wasted time, scanning can assist with getting the correct data upfront. This allows skilled tradesmen to do things right the first time.
A job I did back in 2018 showed this pretty dramatically. We were asked to scan a few stories of an NYC skyscraper. What would have taken two skilled tradesmen 24 hours took the scanner only four hours to complete. Instead of spending those 20 hours tied up in measuring, the tradesmen were able to spend it designing and doing work on the job that required their expertise.
3: Rework
Rework is the bane of every construction project and can be both a time and profit drain. In a survey reported by Autodesk, 70% of rework is the result of bad design. Again, while scanning cannot prevent all design issues it can make sure that the measurements and blueprints that designs are based off are accurate.
In my experience, this is often half the battle. Bad measurements create incorrect blueprints which cause faulty designs and the list goes on. These negative effects trickle down through the construction lifecycle and end up costing thousands in work order changes. By using 3D scanning at the beginning of the timeline to capture the correct measurements, much of this can be prevented.
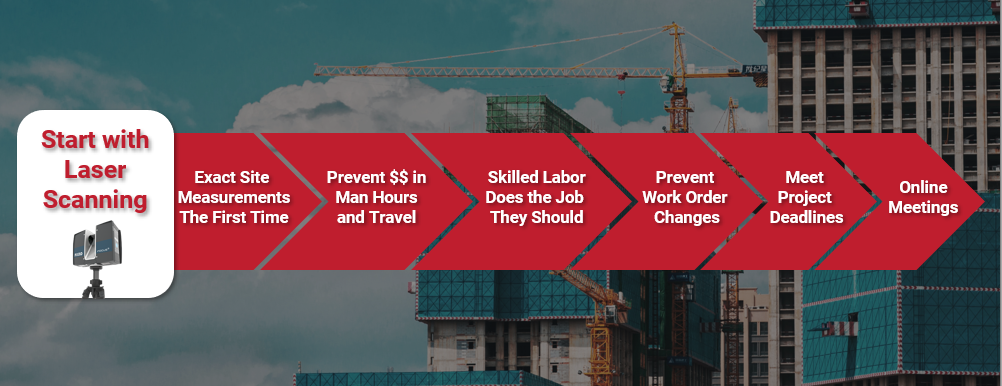
4: Timeline
Time is money, especially when it comes to construction. Sticking to deadlines as put forth by estimates is critical to making a profit. 3D scanning assists in meeting project deadlines in two ways, by first preventing change orders as mentioned above, but also by giving project leads deeper insight into the complexity of the job and allowing them to accelerate timelines.
Recently, one of our clients had a major fire at their manufacturing facility. 33,000 square feet of critical ductwork needed to be repaired due to fire damage. A day after we were contacted, our team visited the facility to scan the area that needed repairs. Using this information, our draftsmen were able to create new designs for the duct in just 2 days. This job could easily have taken two weeks because of how complex it was to measure and design. Thanks to scanning, it became very straight forward and easy to complete.
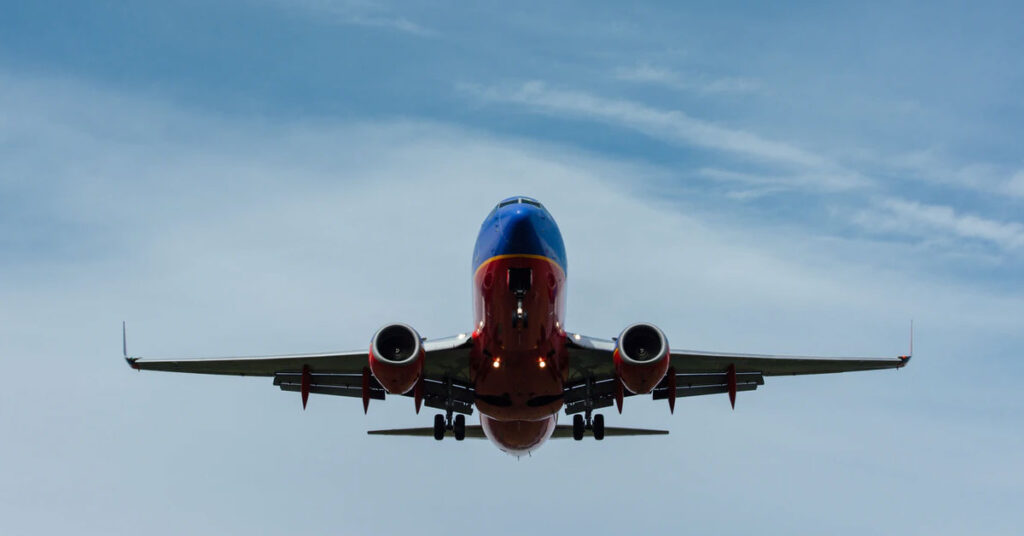
5: Eliminating Travel with 3D scanning
This final bullet is one that has become more important to our clients in recent times. As all of us figure out how to deal with the new normal we are living in, remote work capabilities are no longer a nice to have. By using our 3D scans, clients with teams working on the same project from opposite sides of the country have been able to coordinate jobsite progress. We recently worked with an architectural firm located in Colorado and designing a project in Pennsylvania. The architects were unable to travel to the east coast because of the current situation but were able to create plans with ease thanks to scanning.
If you want to learn more about the technology and see if it is a fit for you, feel free to DM me or reach out to book a demo!